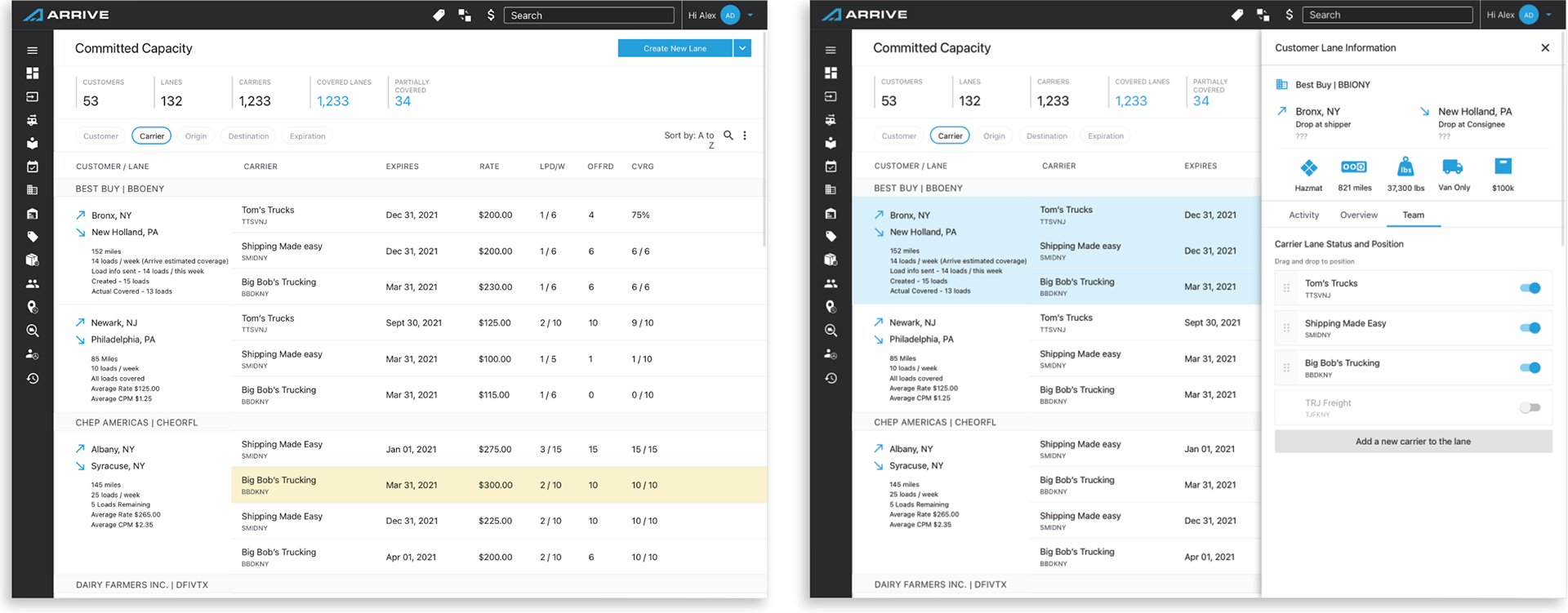
Some initial layouts were produced based off some of the new guidelines and design language. It was prototyped in sketch and presented to the stakeholder for feedback. A problem was that there was not enough density on the screen. A different type of nesting approach was then produced and tested.
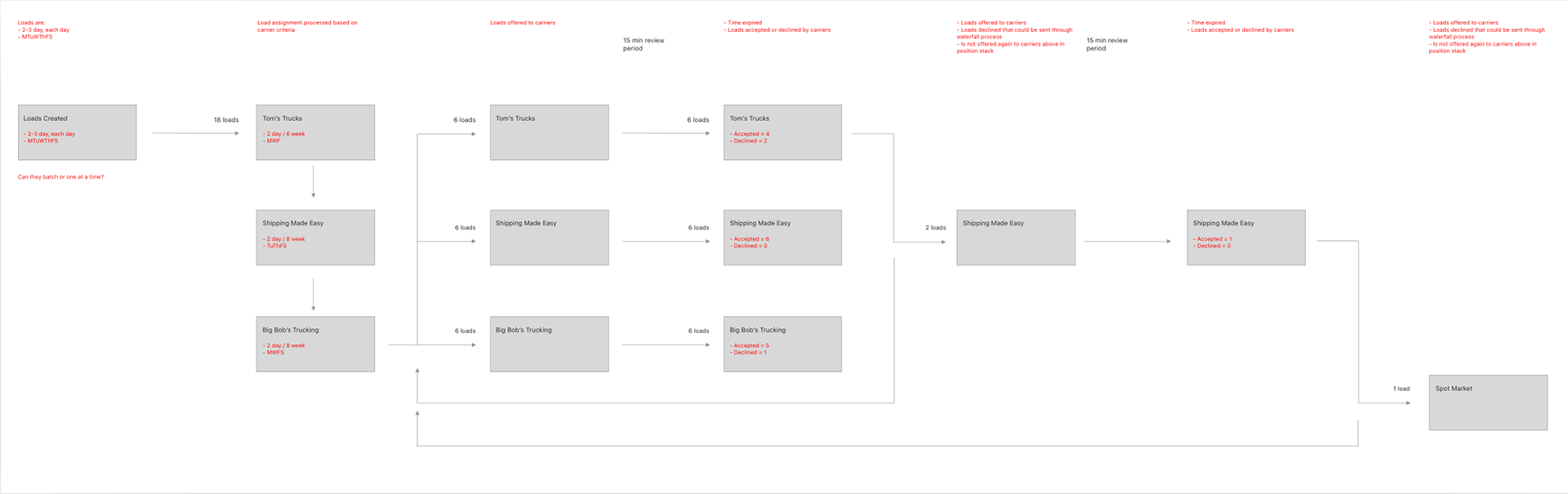
After the initial meetings with the stakeholders, it took time with the PM to sort through the process that the committed capacity back-end system would follow as it issued out loads to committed capacity carriers. This process would ultimately affect aspects of the design, layout, and data shown. This was a documentation artifact outtake from that meeting.
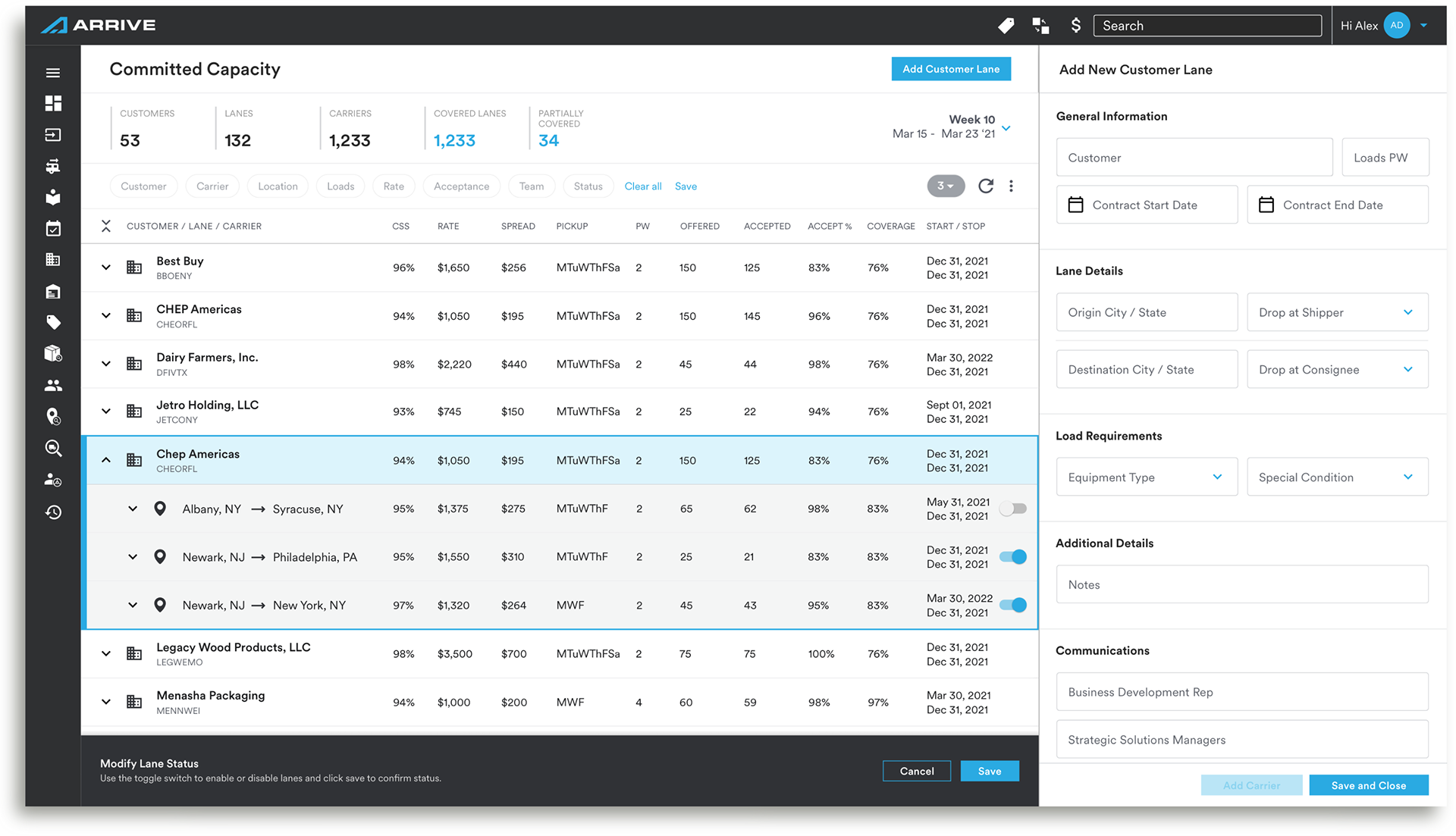
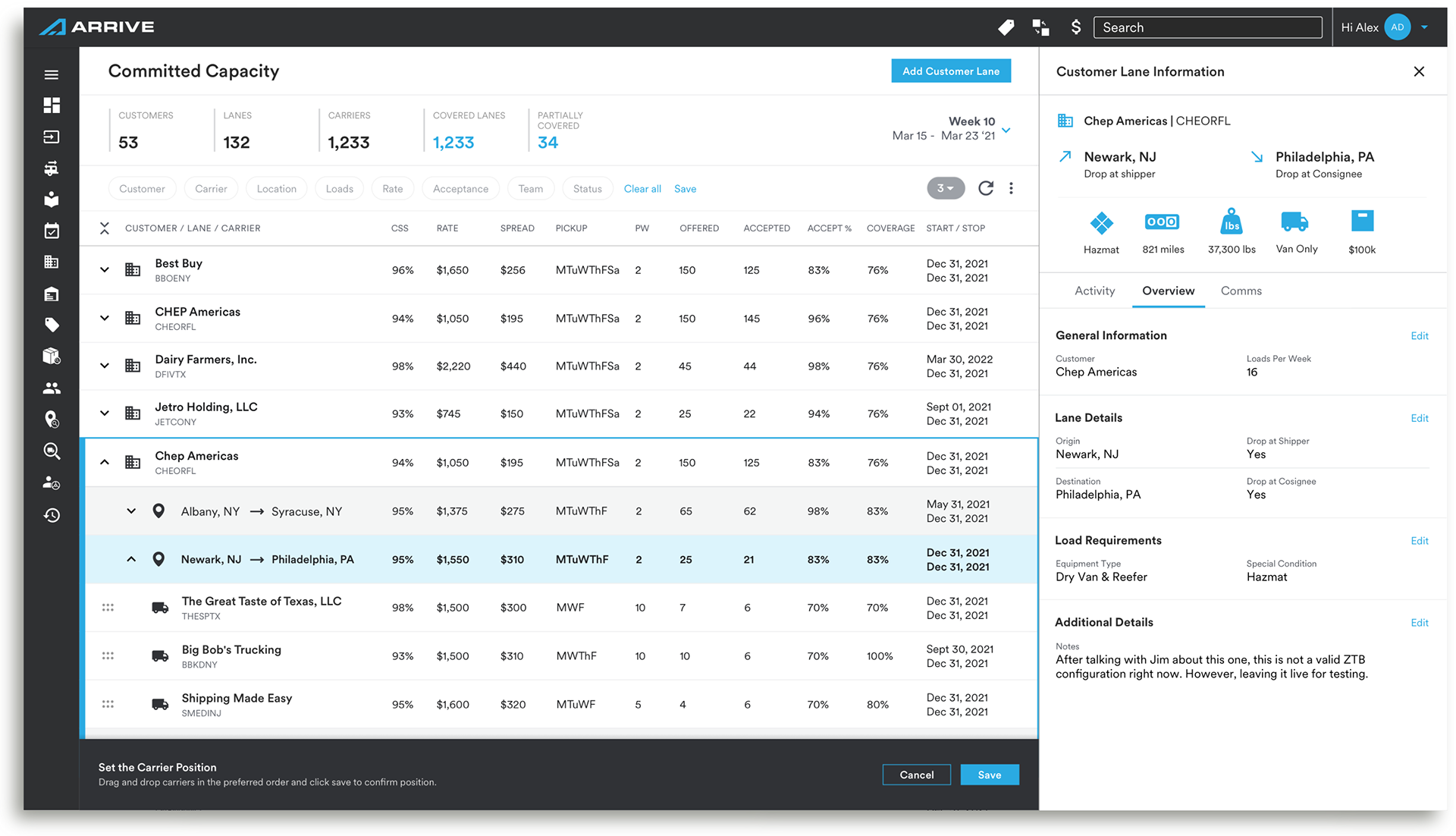
These are some shots from the final design layout that was eventually built for the team. I really enjoyed how integrated everything felt, including the confirmation overlay at the bottom of the screen.
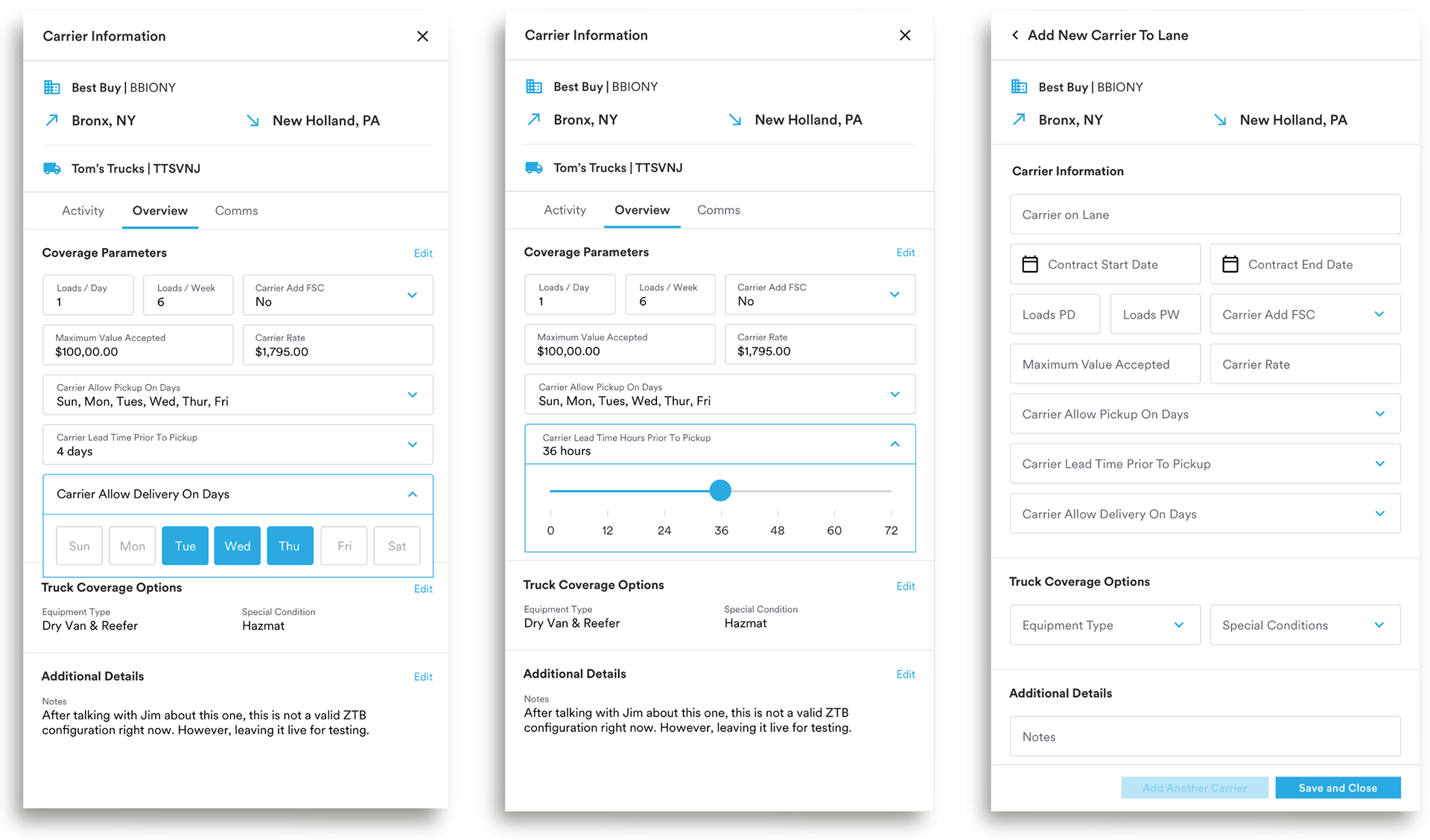
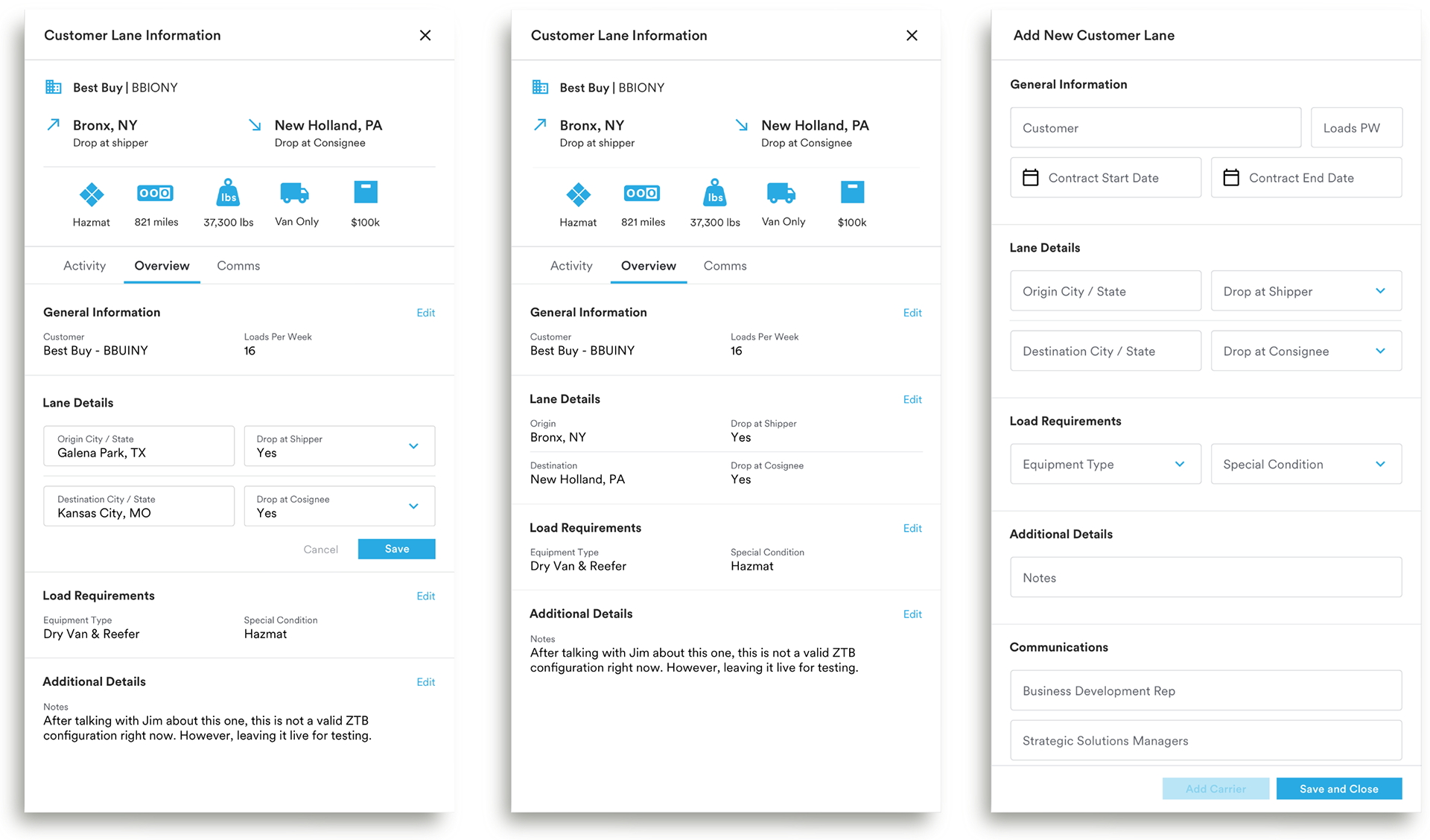
Here are some of the unique side panel layouts that would quickly allow brokers to provide input to all the various parameters and specifics to customers, carriers, and lanes without disturbing the nested dashboard environment.
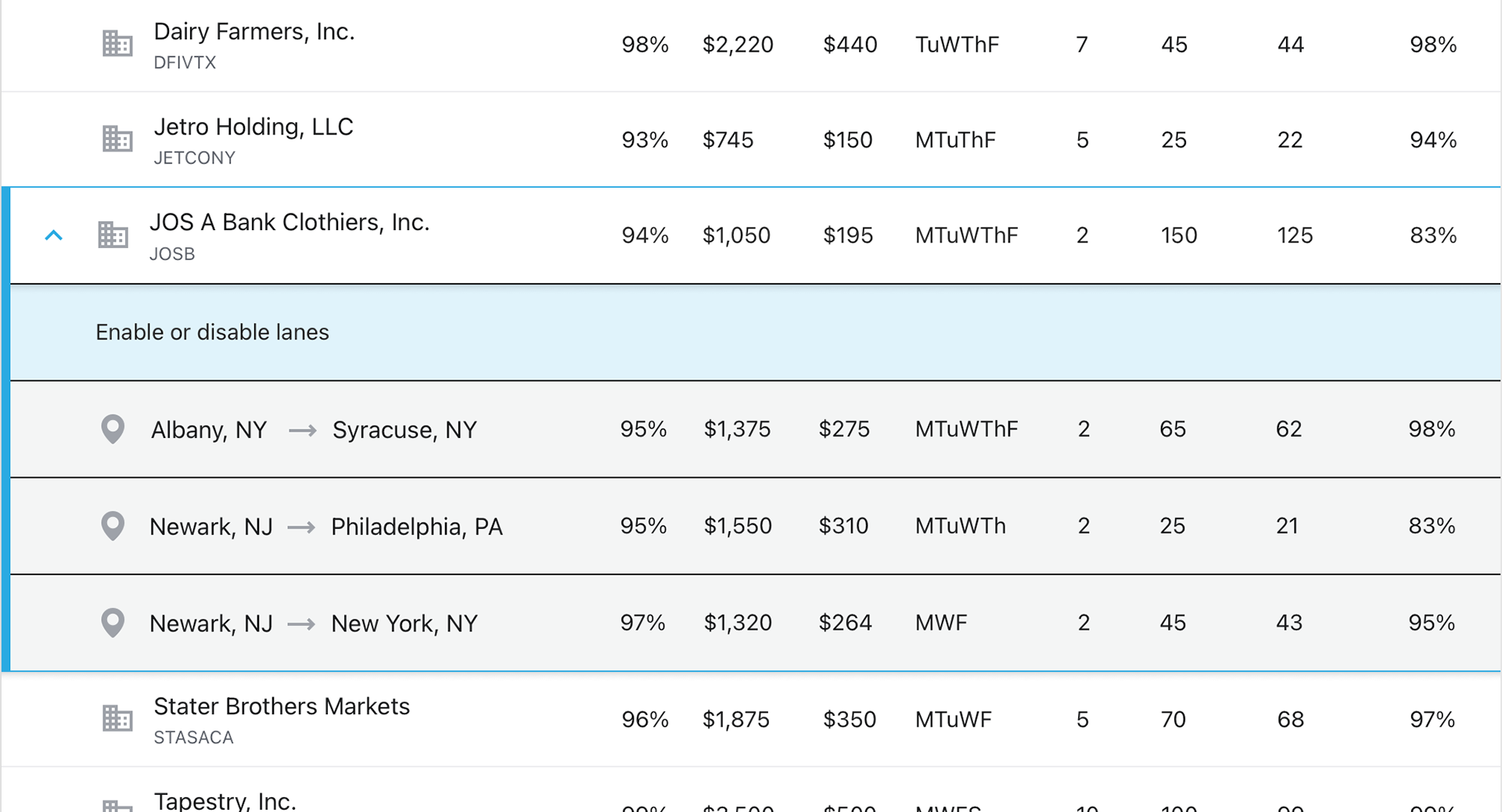
I really enjoy the slight variations in stroke and background coloring to help create depth and focus in the immediate information at hand. This helped the brokers quickly frame and drill down on the specific information they needed to review or update.
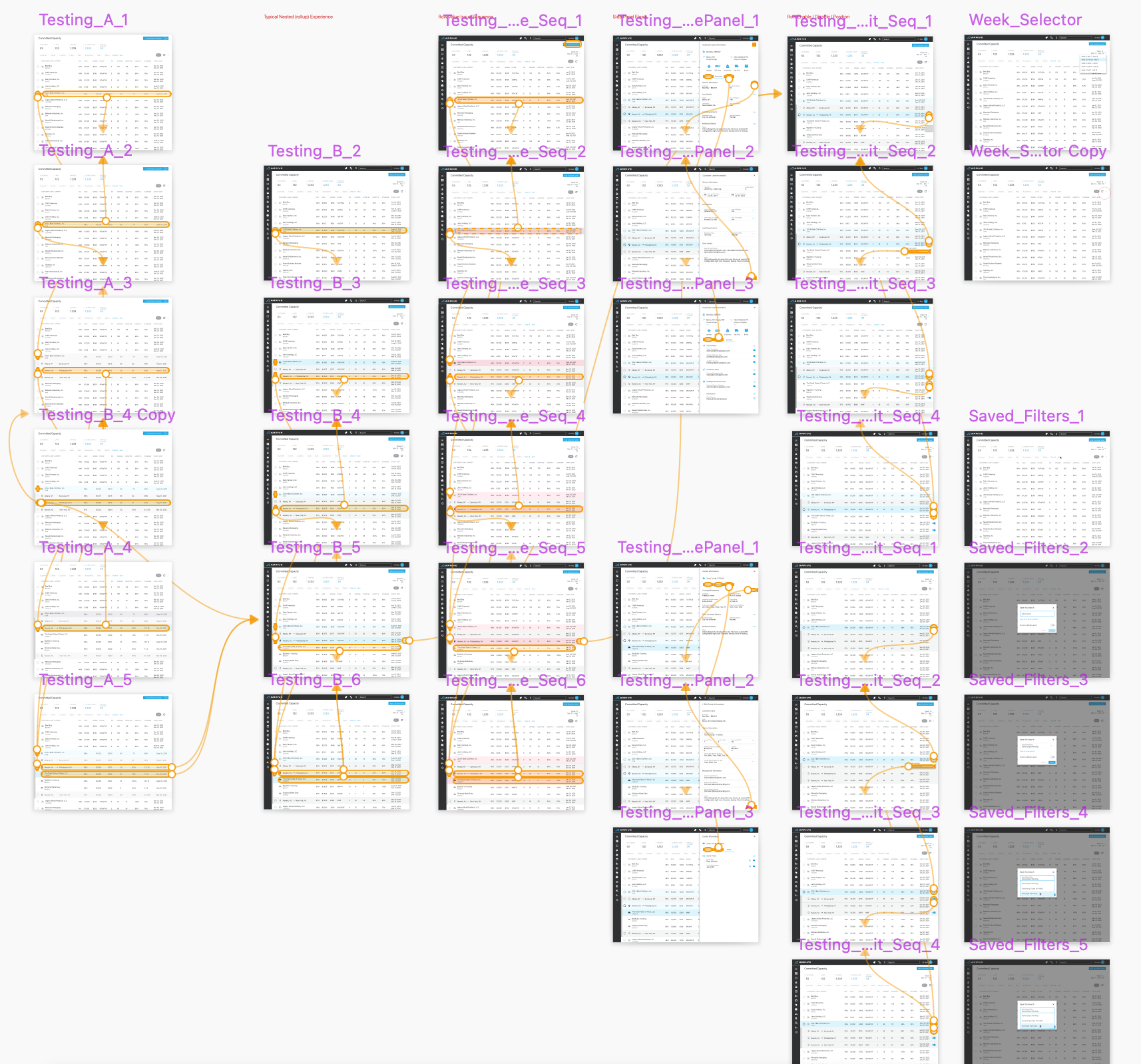
Prototyping in Sketch was a necessary tool to get buy-in from the stakeholders. Prototyping was also a useful way to coordinate intent with the dev team.
Above is a prototype created to test the nesting functionality and coordinate current progress with the stakeholders.